文章內容

Laser Diode (LD)
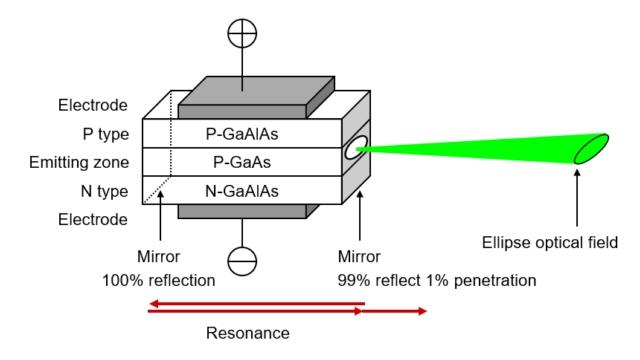
❐ Structure of Laser diode
The structure of laser diode is shown in Fig. 1. The appearance is in a cylindrical form and may have different shapes according to different packaging types. However, the portion that really emits light is only the “die.” The size of a die is almost as a grain of sand on the seaside and such as a small die may emit very strong light. Because the die of laser diode is very small, a piece of 3” GaAs wafer may produce hundreds of dies to be further packaged after dicing. Currently, there are two major types:
➤ Edge Emitting Laser (EEL): The epitaxy plane is in the horizontal direction and will be deposited with a metal reflective film on the left and right sides of the die after dicing. The laser beam will be resonated back and forth along the horizontal direction (in the epitaxy plane) and emitted from the right side, so called Edge Emitting type, as shown in Fig. 1(a). This type of laser has high power, but the projected light field will be in an elliptical shape. Because the core of optical fiber is a regular circle, the energy loss while connecting with optical fiber will be larger.
➤ Surface Emitting Laser (SEL): The epitaxy plane and the metal reflective film are both in the vertical direction. The laser beam will be resonated back and forth along the horizontal direction (perpendicular to the epitaxy plane) and emitted from the epitaxy plane, so called Surface Emitting type, as shown in Fig. 1(b). This type of laser has low power, but the projected light field will be in a regular circle. Because the core of optical fiber is a regular circle, the energy loss while connecting with optical fiber will be less.
Figure 1: Appearance of Laser diode after packaging.
❐ Fabry-Perot laser
If the die in Fig.1 is enlarged, the structure as shown in Fig. 2 may be obtained. The center light emitting zone is a GaAs epitaxy. The P-type and N-type AlGaAs epitaxy are respectively located on the upper and lower sides. There are metal electrodes on the top and at the bottom. After dicing the die, a resonance cavity may be formed by depositing metal films on the left and right sides. When a laser diode is connected with a battery, the electrons will flow into the N-type AlGaAs epitaxy from the negative electrode of the battery, and the electric holes will flow into the P-type AlGaAs epitaxy from the positive electrode of the battery. The electrons and electric holes will be combined at AlGaAs epitaxy in the center light emitting zone and emit light along the left and right horizontal direction. However, the deposited metal film on the left is thicker to form as a reflector (100% reflection) and the deposited metal film on the right is thinner to form as a reflector (99% reflection and 1% penetration). The light emitted from the light emitting zone is reflected back and forth by the left and right reflectors to generate the resonant amplification. Because the reflector on the right is designed for passing 1% of light, the laser beam will be passed and emitted from the right side, as shown in Fig. 2. The structure of this type of semiconductor laser is the simplest, called Fabry-Perot (FP) laser. Because the laser beam is emitted from the edge of the die, it belongs to Edge Emitting Laser (EEL).
Figure 2: Die structure and principle of Fabry-Perot laser.
Because the laser of EEL is emitted from the edge, the shape of edge decides the shape of light field. It may be seen in Fig. 2 that FP laser die is actually a rectangle by viewing from the right, so the shape of light field formed by a laser beam emitted from the right should be rectangular. When the laser travels a distance, the light strength at four corners of the rectangle will be weaker, so the shape of light field will be slowly changed to be elliptical. Because the core of optical fiber is a regular circle, the energy loss will be larger while connecting with optical fiber.
The advantages of FP laser are that the structure is simple and the price is lower; and, the disadvantages are that the light is not pure enough (the emitted light having larger wavelength distribution). Because the optical fiber used in the optical communication industry will have material dispersion, which is resulted from the light of different wavelengths (different colors) will have different speeds while propagating in the same medium, a laser diode must be used to replace LED as the light source at the transmitting end and the purity of light should be the higher the better. Thus, how to make higher purity of light for laser diode should be a very important development direction.
❐ Vertical Cavity Surface Emitting Laser (VCSEL)
The structure of Vertical Cavity Surface Emitting Laser (VCSEL) is shown in Fig. 3(a), which directly employs Molecular Beam Epitaxy (MBE) or Metal Organic Chemical Vapor Deposition (MOCVD) to grow tens of layers of N-type AlGaAs epitaxy on a GaAs wafer, wherein the refractive index for each layer is different; then, growing a layer of GaAs epitaxy as a light emitting zone; growing tens of layers of P-type AlGaAs epitaxy, wherein the refractive index for each layer is different; finally, growing a layer of metal electrode respectively on the upper and lower surfaces of the wafer and using the chemical etching to open a round hold on the upper metal electrode, so the laser beam may be emitted from the upper side. Because the laser beam is emitted from the surface of epitaxy, it belongs to Surface Emitting Laser (SEL).
Figure 3: Die structure and principle of VCSEL.
It can be seen in Fig. 3(a) that each layer of epitaxy of this type of laser is very thin, so the laser beam travels up and down along the vertical direction, generate the resonance between the upper and lower metal electrodes, and is emitted for the round hole on the upper metal electrode, and thus the shape of light field may be kept as a regular circle. Because the core of optical fiber is a regular circle, the energy loss will be less while connecting with optical fiber.
The upper and lower metal electrodes may be applied with voltage, and both may be used as reflectors to enable the laser beam generating resonance. The refractive index for each layer is made different for several layers of different P-type and N-type semiconductors for forming a grating structure along the vertical direction, which may purify the light (with smaller wavelength range). Most importantly, this type of laser needs not to first dice the die and then grow the reflective mirror resonance cavity of metal film, but may directly grow a layer of metal electrode respectively on the upper and lower surfaces of a wafer as the reflective mirror resonance cavity. Thus, a wafer may be simultaneously created with hundreds of laser to form a laser array, as shown in Fig. 3(b), and multiple optical fibers may be respectively connected above each laser and applied in the optical fiber backbone.
❐ Comparison of Laser diode and LED
➤ Laser diode has very small light divergence angle: LED has not resonance cavity, so LED has very large light divergence angle. As shown in Fig. 4(a), the light beam will be rapidly diverged after leaving. Laser diode has a resonance cavity that the light beam may be emitted along the reflector direction, so the light divergence angle is very small. As shown in Fig. 4(b), a laser diode may keep the light beam emitting to a very far place.
➤ Laser diode has very high light purity (very small wavelength range): LED has no grating structure, so it cannot purify the light, as shown in Fig. 4(c). Laser diode has a grating structure to purify the light (making wavelength range smaller), as shown in Fig. 4(d).
Figure 4: Comparison of Laser diode and LED.
The spectrum only having one wavelength for emitted light is indicated by the red curve in Fig. 4(d), but this kind of device is not existed. Actually, human eyes cannot tell if the light is pure or not, because human eyes always can only have the strongest feeling to the light of wavelength with the strongest brightness. If we have to describe the difference between laser beam and light of LED viewed by human eyes, we could only say that when human eyes see a very pure laser beam, the person will be touched beyond words from the bottom of heart. As for what the feeling of “being touched beyond words” would be, this could be only perceived, but not expressed in words!
【Remark】The aforementioned contents have been appropriately simplified to be suitable for reading by the public, which might be slightly differentiated from the current industry situation. If you are the expert in this field and would like to give your opinions, please contact the writer. If you have any industrial and technical issues, please join the community for further discussion.